Modular Construction: The Pros and Cons
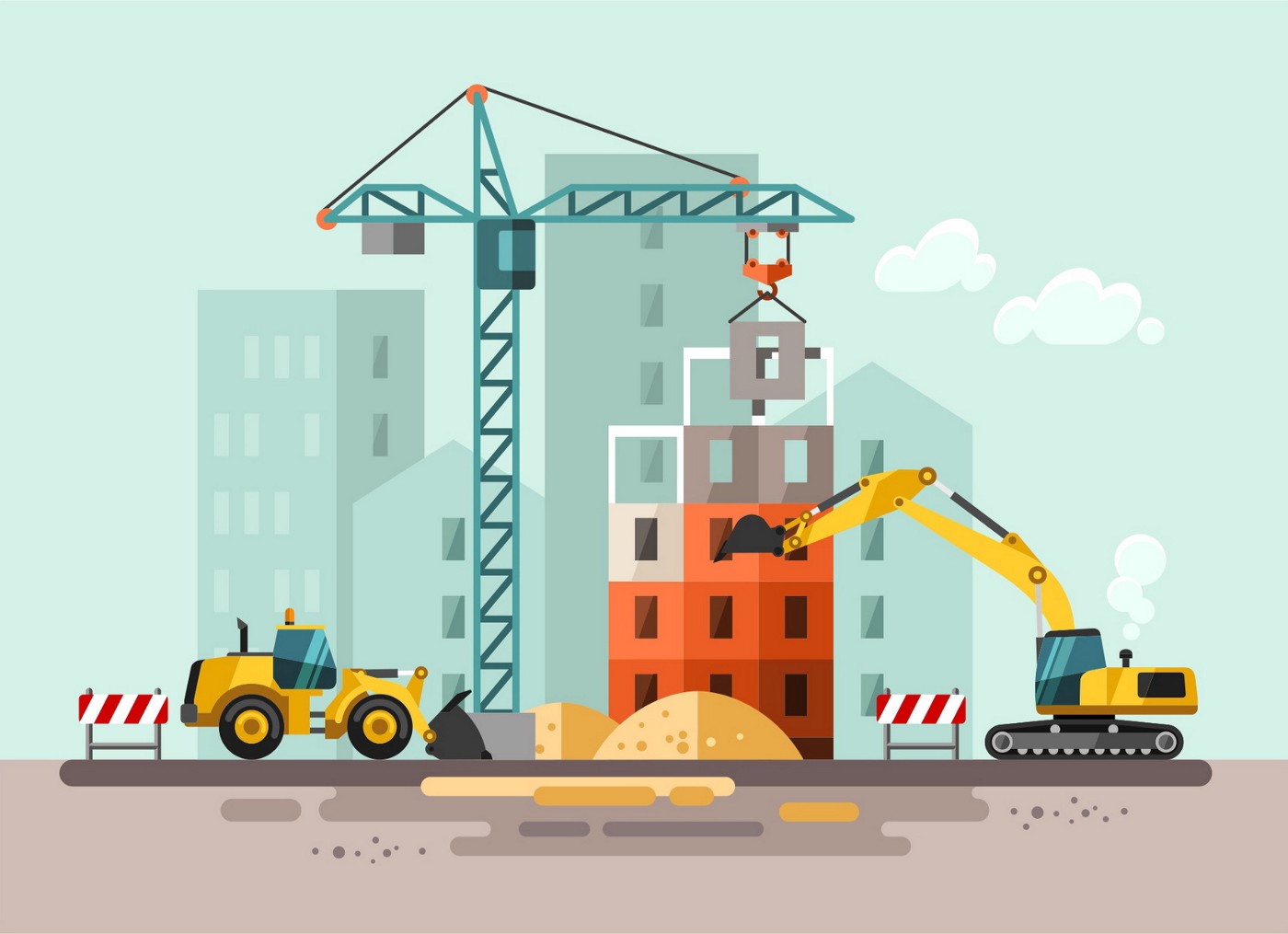
Housing affordability is a growing problem across the nation. New supply of housing has been limited due to rising costs for land, labor, and materials. These rising costs make it harder for real estate developers to build financially feasible projects.
So how can developers lower costs? One potential solution is an evolving construction process called “modular construction.” Modular construction presents a viable solution since, depending on the deal, it can save up to 20% of costs and can be built up to 30–50% faster than traditionally built projects. As the methodology continues to improve, real estate developers can potentially see even more savings.
According to the Modular Building Institute’s 2018 annual industry statistical report, the market share for permanent modular construction in North America increased from 3.18% in 2016 to 3.27% in 2018.
What is modular construction?
Think building blocks that are built in a factory and then brought to the site for assemblage. Each block is called a “module,” which can be a dwelling unit with varying degrees of interior finishes (from shell to fully completed). Modules are built off-site, in a controlled, indoor factory using the same codes and standards as traditionally built projects.
Once completed, modules are shipped on trucks to the construction site and assembled to fit perfectly with each other. Typically, the finished product is designed to look identical to a traditionally built multifamily building. This construction process can be used to build other property types as well — including hotels, offices, retail boxes, etc.
Advantages
- Save Costs: Factory labor is more efficient in an assembly line format and materials can be ordered in higher volumes, cutting out subcontractor overhead.
- Save Time: The factory can build modules concurrently as site and foundation work is underway. Traditional construction can not begin until site and foundation work is completed.
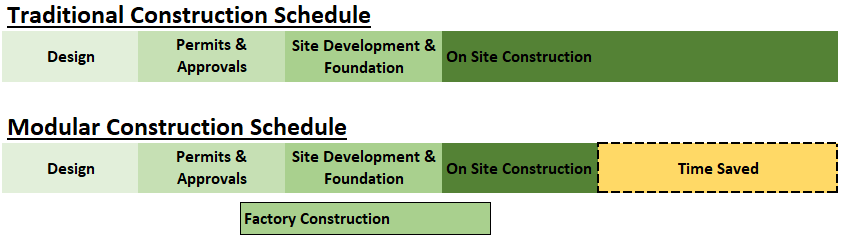
- Save Waste: Materials can be recycled within the factory and the assembly line process leads to more accurate construction.
- No Weather Issues: The factory-controlled setting reduces the risk of delays and damaged materials due to weather.
- Safer: There is less risk of worker accidents since construction occurs indoors and within a structured process.
- Quality Control: Modules are built to meet or exceed the same local, state, and national regulations and codes as traditionally built buildings.
Disadvantages
- Transportation: The factory where modules are built may be distant from the construction site and there are inherent risks in transporting such large loads. The further away the factory is from the building site, the more costly as well.
- Size Constraints: Modules are restricted to the size and capability of the trucks transporting them. Thus, modules are typically restricted to maximum dimensions of 16′ widths and 70′ lengths.
- Site Constraints: An irregularly shaped site may pose design issues since modules are usually rectangularly shaped.
- Organized Labor: Modular projects may encounter opposition from labor unions since more work will go to the factory and there will be less on-site work for labor union members.
- Inflexible: Unlike traditional builds where design updates can be made during construction (where to install electrical outlets for instance), modules are pre-built so making updates once modules leave the factory are difficult.
- Permitting and Inspection Issues: The permitting process may vary state-to-state but in California, the modules are permitted at the state-level and the site-work is permitted by local jurisdictions. Sometimes, local jurisdictions may refuse to accept the state-level permit for module interiors.
Financing Modular Multifamily Construction
Due to the unique construction process, there are additional risks that lenders will evaluate. Every deal is different and will have specific considerations, but three main areas will be capital draws, risk allocations, and team experience.
Construction draws
First, more capital is required earlier since the development timeline is much faster. Lenders will need to accurately project draw schedules in order to calculate the appropriate interest reserve.
Risk allocation
Second, the risk allocations between the general contractor and the modular factory need to be clearly defined when risk is transferred from the factory to the GC. Lenders will want to also assess the financial capabilities of both parties and ensure that proper insurance and bonds are in place.
Experience
Lastly, the team’s strength and experience is very important. Development teams should have a track record of success and should be involved together from the beginning design stage. The design stage is an incredibly crucial part in modular construction because it is difficult to make updates after factory construction has started. Projects should be designed to be modular from the beginning. A developer should not design a project for traditional build and expect that the design can be easily converted to a modular build.
Our expert Capital Advisors help you secure your ideal capital stack, resulting in a lower cost of capital for your investments in less time and with more transparency than a traditional commercial mortgage brokerage. Learn more at StackSource.com.